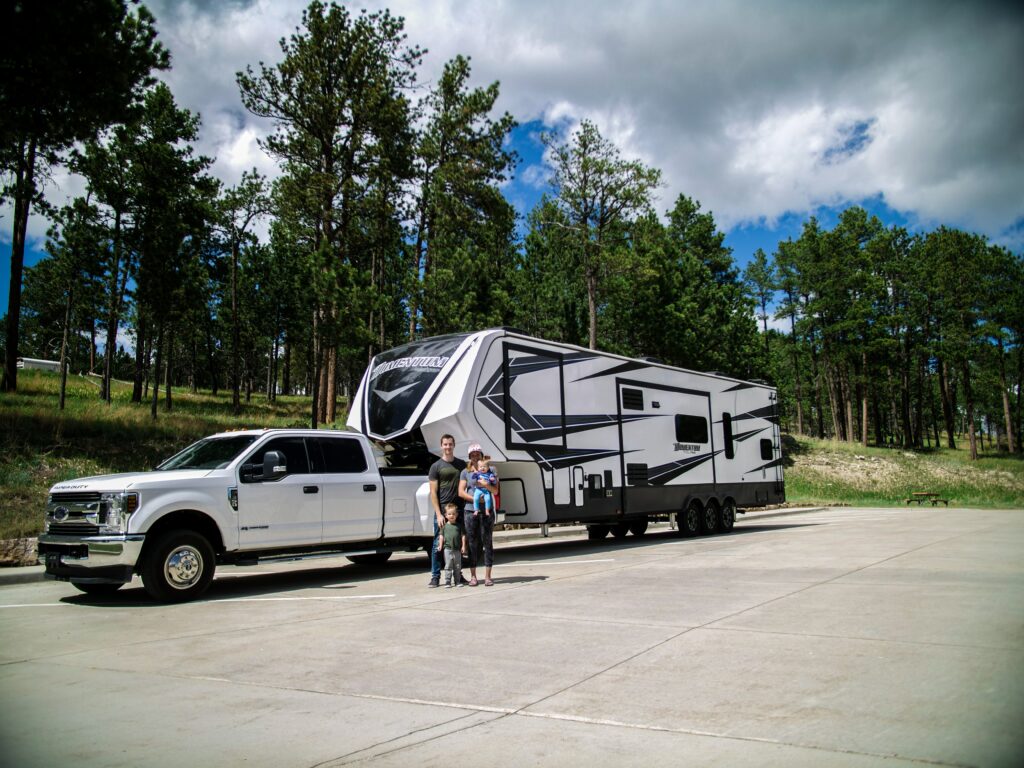
The Complete RV Inspection Checklist for Safe and Smooth Travels: Expert Tips to Avoid Costly Repairs and Breakdowns
Table of Contents
Skipping even one item on an RV inspection can snowball into a repair bill large enough to derail an entire travel budget, or leave you stranded far from help. It rarely begins with anything dramatic. Maybe it’s a faint crack in roof sealant, a tire that’s slightly underinflated, or a propane fitting that is almost tight. Each small oversight has the potential to escalate into water-stained ceilings, shredded sidewalls, or a safety hazard no one anticipated.
Every RV operates as a single, interdependent system, whether a motorhome, travel trailer, or fifth wheel. Routine checks do more than keep the wheels turning. They protect the time, money, and emotion you’ve invested in your RV. By treating the inspection process as a standing priority rather than an afterthought, you protect both the value of the coach and the peace of mind that makes every mile on the road more enjoyable.
Types of RV Inspections & When to Use Them
Every inspection serves a different purpose. By choosing the right checklist at the right time, you’ll catch the issues most likely to surface, without wasting time on the ones that won’t.
1. Pre-Purchase Inspection
- Primary Focus: Structural integrity, hidden water damage, and, on motorhomes, engine and transmission health. A soft wall panel or milky transmission fluid today can become a costly headache tomorrow.
- Recommended Tools:
- Moisture meter to detect damp spots behind finished surfaces.
- Infrared camera for temperature anomalies from wet insulation or delaminating walls.
- Digital multimeter to confirm battery health and uncover wiring issues.
- Flashlight to help you clearly see into dark or hard-to-reach areas during inspections.
2. Pre-Trip Inspection
This is your last line of defense before the wheels roll.
- Primary Focus: Tire pressure and tread, fluid levels, lights, brake operation, lug nut torque, tire date codes (5-7 years old maximum), sidewall condition, and propane safety systems.
- Quick-Grab Tools:
- Tire-pressure gauge (preferably with a dual-foot head for dually wheels).
- Portable propane leak detector to scan fittings and regulator hose.
3. Seasonal Storage Inspection
Whether you are winterizing or getting ready for spring, this checklist keeps your RV safe in the off-season.
- Primary Focus: Winterizing the plumbing, sealing rodent entry points, maintaining batteries, and ensuring ventilation to prevent mold.
- Helpful Add-Ons:
- Compressed-air adapter for blowing out water lines.
- Non-toxic RV antifreeze.
- Dryer sheets and sticky traps for critter control.
4. Professional vs. DIY
Many checks, like routine walk-arounds and fluid checks, are easy DIY tasks. But hire a certified inspector (ideally NRVIA-credentialed or RVTI-certified and ASI-certified for engine and chassis) when:
- You’re evaluating a high-value or complex coach.
- Structural issues or engine diagnostics may become negotiation points.
- Warranty claims need documented third-party verification.
Selecting the right inspection at the right time is the difference between preventative maintenance and surprise repairs. Maintenance isn’t cheap, but it’s always cheaper than repairs – especially when you catch issues early.
Need professional help? Explore our RV Inspection Services.
The Ultimate RV Inspection Checklist
Before stepping inside with flashlights and moisture meters, start where every journey meets the elements: outside. A systematic exterior sweep, from roof to tires, helps you catch water intrusion, structural fatigue, and safety hazards early. Once the shell is sound, interior and systems checks become much more straightforward.
A. Exterior Inspection
Work from the top down so gravity and your eyes can guide the process. Anything that fails above can lead to damage below.
Roof & Seals
- Chalk Test: Rub your hand across the membrane. A white, powdery residue means oxidation; plan a thorough cleaning, reseal, and conditioning treatment.
- Front-Cap Lap Seal (Class C RVs): Run a fingertip along the seam where the cap meets the roof. Any lifting sealant is a potential entry point for water.
Tires & Suspension
With the roof secured, shift the focus to what keeps the rig rolling and level.
- Quarter Test: Insert a quarter into the tread with Washington’s head upside-down. If you see the top of his scalp, it’s time to replace the tire.
- Dry-Rot Scan: Look for fine cracks between tread blocks, especially on tires exposed to the sun during storage.
- Suspension Hardware: Check leaf-spring shackles, U-bolts, and air-bag bellows for rust, wear, or leaks. A compromised suspension can shorten tire life.
Propane System
Next, confirm the fuel powering your amenities is safely contained.
- Soapy Water Check: Brush sudsy water over all fittings. If you see bubbles, you’ve found a leak. Tighten or replace the part before operating any propane-powered appliance.
- Cylinder Date: Check the collar stamp for the manufacturing date. Most cylinders require recertification 10 years after the manufacture date. Some older tanks may show a 12-year interval, but newer tanks follow the 10-year rule. Refilling stations may reject tanks that are past their certification period.
Slide-Outs & Awnings
Finally, evaluate moving parts that often reveal problems only under real-world loads.
- Seal Integrity: Inspect slide seals and sealants any signs of wear, gaps, or tears. Even small pinholes in seals can allow water intrusion, leading to significant water damage over time.
- Awning Fabric and Tension: Fully extend the awning, check for sun damage, and confirm fabric remains taut in light wind.
With the exterior checked and any faults logged, you can turn inward knowing the coach’s first line of defense is ready for the miles ahead.
B. Interior Inspection
With the exterior secured, step inside, where hidden moisture, aging appliances, and neglected detectors can quietly threaten both comfort and safety. Work clockwise through the living space so no cabinet, corner, or closet escapes your attention.
Water Damage
- Moisture Meter Sweep: Check under sinks, around skylights, and along window frames. Readings above 15% may indicate damp insulation or delaminating wall panels.
- Mildew Sniff Test: A musty odor, especially near the floor, often reveals hidden leaks. Trace the scent to its source before mold sets in.
- Floor Flex Check: Step near known weak spots, like doorways or bathroom corners. Spongy flooring signals rot that spreads quickly if ignored.
Also, carefully inspect all corners of the RV at both floor and ceiling levels. Look behind access panels, inside cabinets, and along the floors and walls of each slide room – especially the three interior walls and both sides of the floor.
Appliances
Next, turn to the appliances that keep daily life running smoothly.
- Fridge “Dollar-Bill” Test: Close the refrigerator door on a dollar bill. If it slides out easily, seals may have lost tension, leading to energy waste, or worse, moisture and mold buildup.
- Furnace Trial in Auto Mode: Even in warm weather, lower the thermostat to trigger a cycle. Verify ignition, fan operation, and shutdown sequence. Furnaces that sit idle often fail when temperatures drop.
- Cooktop and Oven Burners: Ignite each burner individually. Uneven flames indicate partially clogged jets that need cleaning.
- Water Heater Check: Fill the water heater and test-fire it using LP gas. Once heated, turn off the gas burner and switch to 120VAC power (if available). Allow 20 minutes to heat, then check that hot water flows from the left side of each faucet. Draw a sample into an insulated cup and measure the temperature – it should be close to 120°F.
Safety Systems
Finally, inspect the systems designed to keep you and your passengers safe.
- Smoke and Carbon-Monoxide Detectors: Units older than seven years (check the date stamped on the back) should be replaced, regardless of battery status. Press the test button to verify audible alarms.
- Fire Extinguishers: The gauge needle should be in the green. Invert and tap the base to loosen settled powder for reliable discharge if needed.
- Egress Windows: Open and close every emergency exit. Sticky latches can cost precious seconds in a real emergency.
With a dry interior, reliable appliances, and up-to-date safety gear, your RV becomes more than road-ready. It becomes a dependable home base for every mile ahead.
C. Systems Deep Dive
With the living space checked, it’s time to lift the hood – figuratively and literally. Electrical, plumbing, and drivetrain systems form the backbone of every RV. Neglect even one, and the most comfortable coach can become an immobile shell.
Electrical
A solid electrical network not only powers your comforts, but it also protects your appliances from premature failure and guards against dangerous shocks. Work methodically, starting at the campground pedestal and moving inward.
- Shore-Power Connection:
- Inspect the plug for heat discoloration; a browned or melted blade points to a loose connection.
- Twist the cord gently; any crack in the sheathing warrants replacement before the next trip.
- GFCI Outlets:
- Plug a simple three-light circuit tester into every GFCI and press the test button. Replace any outlets that fail to trip or won’t reset.
- In older RVs, GFCIs can be tucked behind cabinets. Track them all down to ensure full coverage.
- Battery and Inverter Health:
- Verify resting battery voltage is at or above 12.6 V for flooded lead-acid. Lower readings may indicate sulfation or phantom draws.
- Run a high-draw device like a microwave or coffee pot while watching the inverter output. Voltage should remain between 108 V and 132 V; readings below 108 V or above 132 V may indicate loose or corroded connections, failing inverter, fatigued batteries, or undersized wiring.
- Wire and Lug Inspection:
- Tighten 12-volt lugs to manufacturer-recommended torque. Loose connections can arc under load, leading to melted fuse blocks or, in the worst cases, fires.
Once your electrical systems are safe, shift attention to water. A hidden leak behind a panel can rot floors faster than any electrical short.
Plumbing
Water makes an RV livable, but it can also wreak havoc if left unchecked. Always test the system under real pressure, not just a quick pump burst.
- System Pressurization:
- Fill the fresh water tank and disconnect the city water hose. Turn on the water pump and flush air from every faucet and the toilet. Once the system is fully pressurized and the pump shuts off, turn it off and set a 15-minute timer. When the timer ends, turn the pump back on – if it runs, even briefly, there’s likely a leak in the system. This test uses the pump’s factory-set 40–50 PSI to accurately detect pressure loss.
- Wipe every PEX fitting with tissue; even slight dampness means it’s time to tighten the connection or replace the seals.an O-ring.
- Fittings and Water Heater:
- Inspect the water heater’s relief valve for white calcium tracks. Mineral buildup and scale can prevent proper sealing and over-pressurize the tank.
- Check for rust around the drain plug. Replace the anode rod if more than 75% is consumed.
- Sanitization Schedule:
- Mix ¼ cup unscented household bleach per 15 gallons of tank capacity. Pump the solution through all hot and cold lines, let it sit for four hours, then flush thoroughly until the chlorine scent fades.
- Record the date. Regular sanitizing helps prevent biofilm buildup, which can coat tank walls, clog strainers, and potentially lead to health issues.
With power and plumbing settled, motorhome owners have one more critical inspection layer – everything that turns fuel into forward motion.
Engine & Transmission (Motorhomes)
While drivetrain checks are essential for drivable RVs, a towable owner may wish to check these items on their tow vehicle prior to a trip to ensure safe and reliable towing.
- Fluid Analysis:
- Draw small samples of engine oil and transmission fluid and send them to a lab such as Blackstone. Accurate fluid analysis is most effective when done at consistent service intervals, as it helps identify sudden or drastic changes over time. Elevated silicon levels can suggest dust ingestion, while copper or lead traces may indicate early bearing wear – often well before audible symptoms occur. When inspecting a used unit for purchase, unusually high readings on a first sample could warrant a more thorough drivetrain inspection.
- Visual and Level Checks:
- Inspect the coolant for the correct color – any “chocolate milk” swirl signals contamination. Verify the overflow reservoir tank is within the safe range.
- Examine drive belts for glazing or cracks; cracked ribs can lead to a sudden breakdown, leaving you stranded miles from help. Also check for proper tension – belts typically stretch about 1% during break-in and may fail once they reach 2%. If any belt shows an inch or more deflection when pressed with your thumb, it should be inspected closely.
- Hot-Skin Voltage Test:
- With the engine off and the RV connected to 120VAC shore power, connect a multimeter lead to an unpainted chassis point and the other to damp ground. If your test shows any AC voltage, no matter how small, it’s a sign of stray current, which should be addressed promptly. There is no safe minimum other than 0.0 VAC. Trace the wiring and grounds until the voltage drops to zero.
- Exhaust and Intake:
- Start the engine and let it run until it reaches its normal operating temperature. A visible puff of blue or white smoke may indicate oil consumption, while black smoke under the throttle suggests a clogged air filter or injector issues. However, greyish-white vapor is simply moisture and humidity causing condensation and is typically normal.
Electrical, plumbing, and drivetrain reviews may feel tedious, but they are essential for avoiding vacation-ending failures. With stable power, sealed water lines, and a healthy engine, your RV is ready for any challenges you may face on the road with confidence.
Advanced Tools & Smart Hacks
The core checks above cover every major failure point, but a few modern gadgets can help enhance your awareness, shorten troubleshooting time, and catch problems that may still escape visual inspection.
Infrared Thermometer
- After a short drive, scan each brake drum or rotor using an infrared thermometer or a compact thermal camera, such as a micro FLIR unit that attaches to your phone or tablet. These tools are ideal for walk-around checks and can reveal issues like loose or damaged wiring, fluid leaks, or overheated components long before they become emergencies.
- On travel days, a quick scan at all fuel stops offers early warning long before smoke or odor alerts you.
- Never use your hands to check hub or drum temperatures, as surfaces can reach up to 400°F even under normal conditions, posing a serious burn risk. Instead of looking for a specific number, watch for temperature differences between components – significant variation may indicate a dragging brake, sticking caliper, or under-lubricated bearing.
Wi-Fi Endoscope
- Use the flexible camera to inspect wall cavities, around water heaters, or inside underbelly corrugations. A brief sweep uncovers rodent nests, loose wiring bundles, and early mold growth without removing a single panel.
- Most models stream video to a phone, letting you capture still images and mark problem areas for future repairs or warranty claims.
RV-Specific Mobile Apps
- TireSafe integrates with many aftermarket TPMS systems, delivering real-time pressure and temperature data directly to your dashboard or smartwatch.
- RV Checklist lets you build personalized pre-trip and storage checklists that can be synced across family devices – because more eyes on the process means fewer missed latches, vents, or valves.
These compact tools require little storage space yet add a professional edge to any DIY inspection routine, turning good maintenance habits into truly preventive care.
Regional Considerations
Even the best toolkit can’t override climate. Tailor your inspection routine to the environment your rig calls home, and you’ll stay ahead of regional wear patterns that standard checklists often miss.
Coastal Areas – Guard against Salt
- Chassis and Brake Corrosion: Salt-laden air deposits chloride crystals on metal surfaces. Inspect frame rails, brake calipers, and step brackets for flaking rust. Wire-brush affected areas and apply a rust converter as needed.
- Electrical Connectors: Salt creep accelerates galvanic corrosion. Apply dielectric grease to Molex or plastic connector plugs, battery terminals, and leveling-jack connectors.
- Exterior Wash-Down: Rinse the undercarriage with fresh water after every seaside trip. A fifteen-minute rinse now prevents costly sandblasting later.
- Hinges, Latches, and Locks: Sand in hinges, latches, and locks is another coastal issue. Rinsing and relubricating them helps maintain smooth operation and prevent premature wear.
Southwest Deserts – Beat the UV Barrage
- Seals and Gaskets: Apply a UV-blocking conditioner like 303 Protectant to slide seals, window gaskets, and roof vent covers every 30-90 days. Chalky residue on the cloth means oxidation has already begun.
- Tire Sidewalls: High UV and hot asphalt accelerate dry rot. Cover tires during long stays and confirm DOT date codes, and replace tires at seven years regardless of tread depth. Additionally, rolling the tires up on wooden or plastic pads help to slow the oxidation process.
- Plastic Components: Porch-light lenses and skylights turn brittle over time. A quick tap test can reveal spider-web cracking, indicating the need for proactive replacement. 303 and other UV blockers can also extend the life of plastic components, helping them resist sun damage and stay flexible longer.
Midwest & Northeast – Winters that Test Plumbing
- Compressed-Air Blowout: After draining the water heater, connect an air hose to the city water inlet and use 30–50 PSI to push air through the system. Open all faucets and low-point drains to evacuate as much water as possible. Once the lines are cleared, add RV antifreeze to ensure full freeze protection—any residual water left in the system can dilute the antifreeze, reducing its effectiveness. Even a slushy mix can expand enough to damage fittings, valves, or faucets, often leading to slow leaks or dripping taps.
- Hidden Valves and Filters: Remove canister filters and bypass outdoor shower valves; both can retain water beyond the reach of standard pump purges.
- Battery Stewardship: Cold temperatures significantly reduce battery performance. Store lead-acid batteries indoors on a maintainer to preserve charge. Lithium batteries should be stored above freezing and never used below 35°F unless equipped with a heating system. Always follow manufacturer guidelines for safe storage and operation.
You Can Find Us in These Service Locations
At Good Sam RV ProCare, we share your love for the camper lifestyle and RV living. Give Us A Call at 833-782-2731 or find our mobile RV services in the following locations:
Stay Road-Ready: Final Thoughts Before You Roll
A thorough RV inspection isn’t just about preventing costly repairs; it’s about preserving your freedom on the road. From the roof seals to the brake rotors, every part plays a role in keeping you safe and mobile. By following this comprehensive checklist, you reduce the risk of unexpected failures and protect your investment long-term. Whether you’re prepping for a cross-country adventure or seasonal storage, consistent attention to detail helps ensure every journey starts – and ends – on a high note. Ready to roll with confidence? Let this checklist be your guide, mile after mile.
Frequently Asked Questions (FAQs)
Will DIY inspections void my warranty?
No. U.S. warranty law allows owners to perform routine checks, as long as factory-specified parts and fluids are used. Be sure to document your findings with dated photos and parts/materials receipts (if applicable) to support any future warranty claim.
How do I find a certified inspector?
Search the National RV Inspectors Association (NRVIA) or RVTAA directories by ZIP code. For drivetrain or generator assessments, look for an inspector with Level 2 certification.
Can I inspect an RV remotely?
Yes. Many NRVIA-certified inspectors offer virtual walk-throughs via video call. They typically provide moisture-meter readings, infrared images, and a detailed written report so you can assess the RV from anywhere.